...to use up, my apologies. Some years ago I took Loren Stump's intensive course, which among other things included making face canes. His idea was to plop a can on the front of your bead, pluck out the nose (and rebuild it with plain background glass.)
Round about this time two conditions prevailed that no longer apply. One was that mermaid beads were all the rage. (Remember those?) The other was that all those luscious greens and other hand pulled colors Mike Frantz has inviegled Effetre into producing for obscene amounts of money were not available, at least not in the opaque green pallette. Jan Burrows of Check Glass did and continues to have the most yummy assortments of blue-greens.
Alas, the rather yellowish green I selected for my base is an extremely evil, shocky glass. Not as evil as pig, but totally and completely unsuitable for making cane, since it has this tendancy to shatter once the inch or so projecting into the kiln is used up. —That is, like some bullseye, the temperature difference between molten and room temperature glass, if spread linearly over less than an inch or so, just causes the molten end to crack and fall off the rod. Jan sold me some thinner stuff some years back, and I remember trying it and coming to the conclusion it was just as bad.
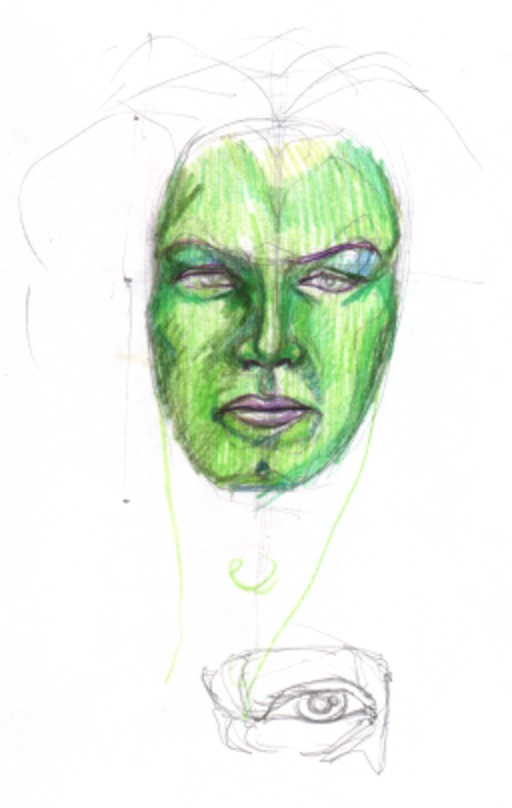
refinement of face cane idea. Colored pencil, 1999. Yeesh, that drawing ain't very symmetrical, is it? No wonder my glass isn't either.
And to make matters even more aggravating, when I mixed the nominally compatible czech and effetre opaque greens together, my stripeys occasionally cracked; and about six months ago, some trailing incorporating these czech opaque greens popped off this beloved bead, which was pretty disspiriting, cuz I made the bead years ago, and figured it was now safe from these problems. The czech glass was also well under the 15% rule, which didn't bode well either.
So I stopped using the glass in my work altogether for several years.
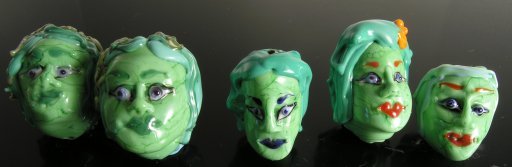
Five green sculptural heads, presented in order of manufacture (l-r). Czech soda lime glass, with some effetre accents, all hollow, built on 3/32 mandrels with flame-dri release. March (? also Feb) 2007. Tallest, 38mm, 27mm wide, 28mm deep.
This is actually the third set of beads I've made in this series: I started with brown (big mistake) and then ivory, which I'll feature later, but I knew I needed a lot of practice, and figured I might as well practice on the green glass, since it wasn't suitable for much else. It's not even particularly suitable for faces, since compared to ivory it's extremely heat sensitive: of these beads, I believe at least three of them have cracked. I've become something of an expert at repair, following the lead of fellow beadmaker Joy Cichewicz, who simply pops her big sculpturals back in the kiln if they crack, and repairs them.
I find that my boro annealing schedule works well for this purpose. It has a striking step currently set at 1150 deg F, which preheats even this shocky glass sufficiently that it's fairly easy to bring it into the flame. The cracks typically appear on the neck, the back or the top of the skull, so they're pretty easy to melt in, provided the bead is still on its original release. I had one crack appear, or so I believe from taking the (hollow) annealed bead out of the kiln at 400 or so, glancing at it, and letting it finish cooling to room temperature in a fiber blanket. Since the crack appeared nowhere near the tiny amounts of effetre applied (for eyes and mouth) on the nape I'm forced to conclude the problem was thermal shocking, which tells me this particular color is touchy indeed (and possibly the reason why my stripeys cracked—I often take production beads out of the kiln once they're well below the strain point and air cool them, but this glass simply may not tolerate this—at least, not when mixed with other colors. It would be interesting to do some tests.)
The other thing I do, which is a useful trick for ivory as well, is after shaping the back of the skull and the basic face is to paint (as for strip casing) cheekbones, jawlines and brows. This covers up the veining that comes out of the opacifyers separating when you heat the bead up hot initially to round it. My other secret weapon is a No. 5 forceps, known to us stringers as a knotting tweezer. I'll go into the use of this tool in a future post.
file created 14mar07.
Unless otherwise noted, text, image and objects depicted therein copyright 1996--present sylvus tarn.
Sylvus Tarn