Here is the very first “large” (as in, over an inch, or 36mm at its widest dimension) button with a glass shank. It will have to pass the Posy-Approval Test first but I did make it with the idea of selling it to someone.
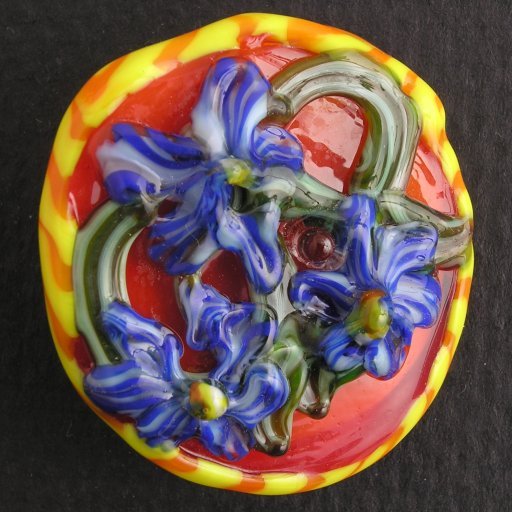
Effetre soda lime glass, 36mm at widest point. Glass shanked button, Feb2006. Note dot or hump nestled between two of the flowers. This is what is technically known as a punty scar.
This, despite its lack of roundness and uneven twistie application (see end note) which would mark it way, way, way down on any bead I tried to sell.
But Posy PATted me with assurances like ‘it's handmade. It's completely different. I showed it to people and they loved it.’ Ok, I guess I can buy the charming folk-art quality argument.
Besides I'm getting to practice my twisty skills (heaven knows they need it), and I love making florals.
How I made this one
Not thrilling reading, not especially useful (I discarded this method after two buttons) just pure self-indulgent chatter. Which is why it's at the bottom of the page.
I'm rather comical, making these things, because after the standard drooping a glob of glass and flattening it, and putting another glob of transparent on to case, and mashing, my pair of disks, like a badly made sandwich, never quite line up. (Except, the filling—the flowers and leaves—goes on top:) Hence the twisty coverup.
In fact, with these early efforts, I was so inept I would next put (ahem) a button of glass on the back and sink a boro puntile into that to give a handle at right angles. (Why not just continue to hold the rod with the pancake on the end of it? Well, because. —That is, I when I tried using the rod as a handle to warm the disk I flipped it along the long axis, like a lollipop. On the boro puntile, it turned like a wheel on a car—more like making a bead.)
At this point, I had to have the overall shape and flatness done, because I could no longer mash, what with the punty smack in the middle. After putting on the leaves and flowers, I would cover up my uneven edges with even more unevenly applied twistie (and what does this tell you, O student of lampworking? Yes, indeedy, I was working too hot. And why would I, who espouse never using more heat than needed do this? Cuz my previous efforts would get too cool and crack, the rotten things! It's called not being able to read the heat base: I'm used to hollow spheres 10–13mm in diameter, not flat disks 25mm+ wide and 6mm thick).
Then, having gone to all that trouble to put the rotten thing on a boro puntil, I had to then remove it, by puntying up from the front with effetre (hence the scar) and then heat the boro puntile (this usually involved some grumbling and picking out boro chunks left behind) and attaching the little (pre-made, and waiting in a 980deg kiln) seed bead for the shank.
Yeah, more than you wanted to know. But how will I be able to trumpet how much better I'm doing it now if I don't make you suffer with my early approaches? Stay tuned for the next thrilling installment!
file created 09mar06.
Unless otherwise noted, text, image and objects depicted therein copyright 1996--present sylvus tarn.
Sylvus Tarn